Understanding Lathe Machine Parts for Optimal Metal Fabrication
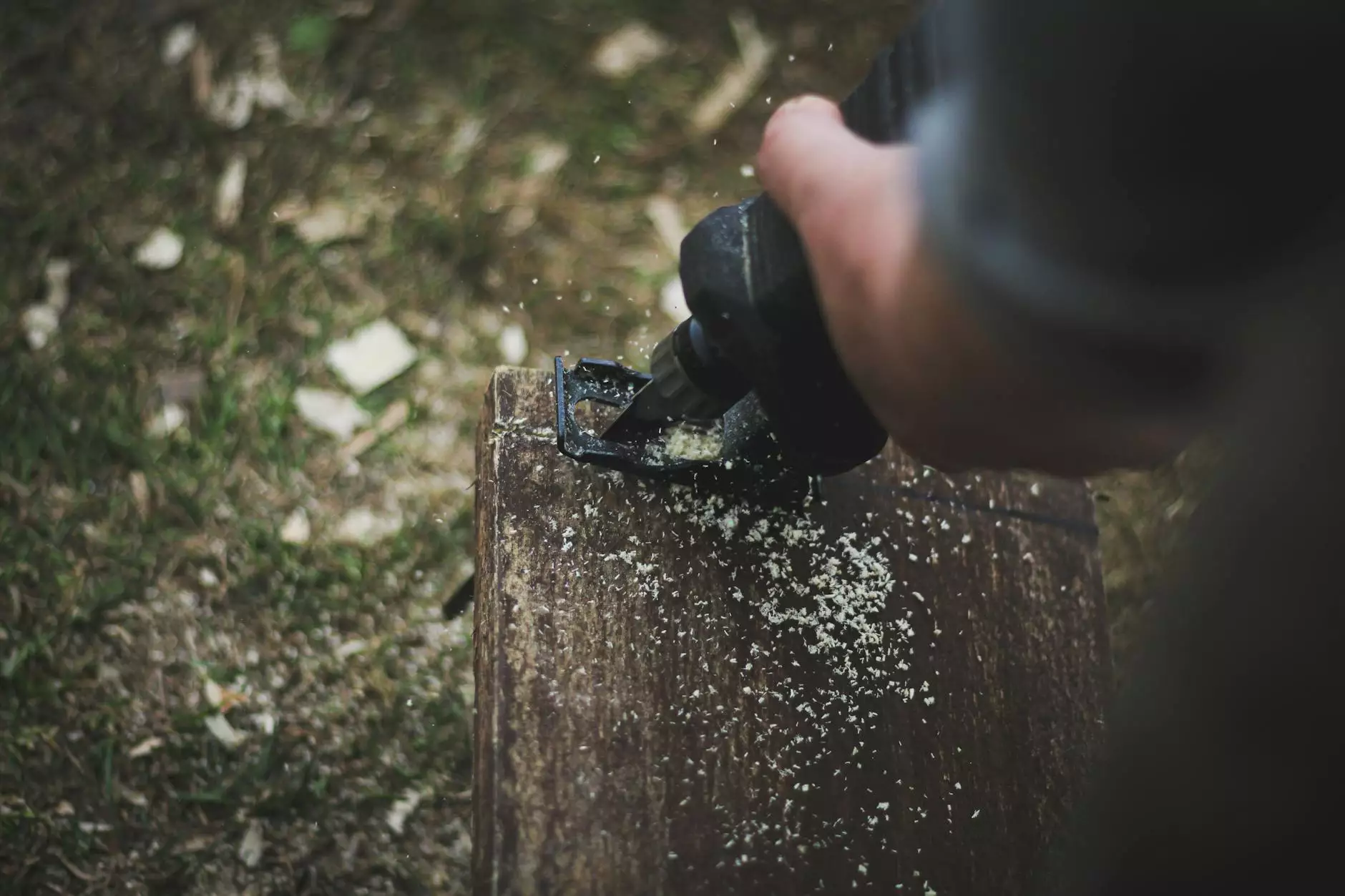
In the world of metal fabrication, lathe machine parts play a pivotal role in ensuring precision and efficiency. These components are integral to various manufacturing processes, allowing businesses to convert raw materials into high-quality products. This article delves into the essential aspects of lathe machine parts, their functions, and their significance in metal fabrication.
The Importance of Lathe Machines in Metal Fabrication
Lathe machines are crucial in the manufacturing industry, particularly in metal fabrication. They are designed to remove material from a rotating workpiece to produce intricate shapes and features. Understanding how lathe machine parts function is essential for optimizing production and ensuring quality. Here are some reasons why lathe machines are invaluable:
- Precision Production: The accuracy of lathe machines enables manufacturers to meet exact specifications.
- Versatility: Lathe machines can be adapted to work with various materials, enhancing production flexibility.
- Efficient Material Removal: They efficiently remove material, reducing waste and production time.
- Complex Shapes: Lathe machines can create intricate designs that would be difficult to achieve with other equipment.
- Consistency: Consistent results are achieved, critical for mass production scenarios.
An Overview of Lathe Machine Parts
To fully appreciate the functionality of lathe machines, it is essential to recognize the various parts that make them up. Below are the primary components of lathe machines:
- Bed: The base of the lathe that supports all other components and provides stability.
- Headstock: Houses the spindle, motor, and other mechanisms to control the speed and movement of the workpiece.
- Tailstock: This part supports the opposite end of the workpiece and can be adjusted to accommodate different lengths.
- Carriage: Holds the cutting tool and moves it along the workpiece, allowing for various cutting operations.
- Apron: Attached to the front of the carriage; it contains controls for operating the lathe, such as feed controls.
- Cross Slide: Moves the cutting tool in a direction perpendicular to the rotation of the workpiece.
- Tool Post: The part that holds the cutting tool securely in place while machining.
- Chuck: A clamping device that holds the workpiece during machining.
Key Functions of Each Part
Understanding each lathe machine part's role can enhance operational efficiency and improve product quality. Let’s delve deeper into the functions of these components:
1. The Bed
The bed serves as the foundation of the lathe, ensuring stability. It is typically made of heavy cast iron to minimize vibrations during operation, which can affect accuracy. A quality bed design contributes significantly to the overall performance of the machine.
2. The Headstock
The headstock is responsible for driving the workpiece and controlling its rotational speed. It contains precision components such as gears, pulleys, and a spindle, allowing the operator to achieve the desired RPM (revolutions per minute) based on the material being machined.
3. The Tailstock
This component is adjustable and supports long workpieces, enhancing the machine's versatility. The tailstock can also be equipped with a drill chuck to enable drilling operations on the workpiece.
4. The Carriage
The carriage is critical for moving the cutting tool over the workpiece. It can be moved manually or powered, allowing for precise adjustments during operation, which is essential for intricately designed components.
5. The Apron
The apron brings the necessary controls closer to the operator, allowing for easy manipulation of the lathe during operation. It usually features levers and switches for controlling movement.
6. The Cross Slide
The cross slide facilitates movement perpendicular to the workpiece's rotational axis. This function is vital for achieving precise diameters and shapes on the material being worked on.
7. The Tool Post
As the part that holds the cutting tool, the tool post's stability is critical for accurate machining. Different types of tool posts may be employed depending on the complexity of the task.
8. The Chuck
The chuck securely holds the workpiece in place during operation. Different types of chucks, such as three-jaw or four-jaw, can be used depending on the shape and size of the workpiece.
Advantages of High-Quality Lathe Machine Parts
Investing in high-quality lathe machine parts can vastly improve production outcomes. Some advantages include:
- Increased Longevity: Durable components lead to less frequent breakdowns and replacements, saving costs.
- Enhanced Performance: Superior parts improve the machine's overall performance and output quality.
- Improved Safety: High-quality parts minimize operational hazards, ensuring a safer work environment.
- Better Support: Quality parts often come with better manufacturer support, crucial for maintenance and repairs.
Choosing the Right Lathe Machine Parts
Selecting the right lathe machine parts can significantly impact productivity and product quality. Here are some tips for making informed decisions:
1. Assess Your Needs
Understand the specific requirements of your operations. Different applications may necessitate other types of lathes and parts.
2. Consider Material Compatibility
Ensure that the parts are compatible with the materials you are working with. For instance, some parts may wear out faster when machining harder materials.
3. Look for Quality Suppliers
Partnering with reputable suppliers is crucial. Quality vendors often provide parts that come with warranties and reliable customer service.
Maintaining Lathe Machine Parts for Longevity
Regular maintenance of lathe machine parts is key to maximizing their lifespan and performance. Here’s how to effectively maintain these components:
1. Regular Cleaning
Dirt and debris can affect the accuracy and performance of the lathe. Regular cleaning helps maintain optimal functionality.
2. Lubrication
Proper lubrication reduces friction between moving parts, preventing wear and tear. Follow the manufacturer's recommendations on lubricants and intervals.
3. Regular Inspections
Conducting routine inspections can help identify potential problems before they become severe issues. Check for wear, alignment, and any necessary adjustments.
Future Trends in Lathe Machine Technology
The future of lathe machines promises exciting advancements. Here are some trends that are shaping the industry:
1. Automation and Robotics
Integrating automation into lathe operations will enhance efficiency and reduce labor costs. Robotics may manage repetitive tasks, allowing skilled operators to focus on more complex processes.
2. Smart Technology
Smart sensors and IoT connectivity are set to revolutionize machine monitoring and maintenance, providing real-time data on machine performance and predictive maintenance options.
3. Advanced Materials
As materials science progresses, lathe machines will increasingly work with advanced alloys and composites, demanding new adaptations in machine design and parts.
Conclusion
Lathe machines are indispensable in the metal fabrication sector, thanks to their versatility and precision. Understanding lathe machine parts and their functions is essential for operators and business owners alike. By investing in high-quality parts, engaging in regular maintenance, and keeping an eye on the latest industry trends, manufacturers can optimize their productivity and quality.
For more detailed information about the best lathe machine parts and their applications in metal fabrication, visit deepmould.net.