Understanding the Importance of Prototype Molded Parts in Modern Manufacturing
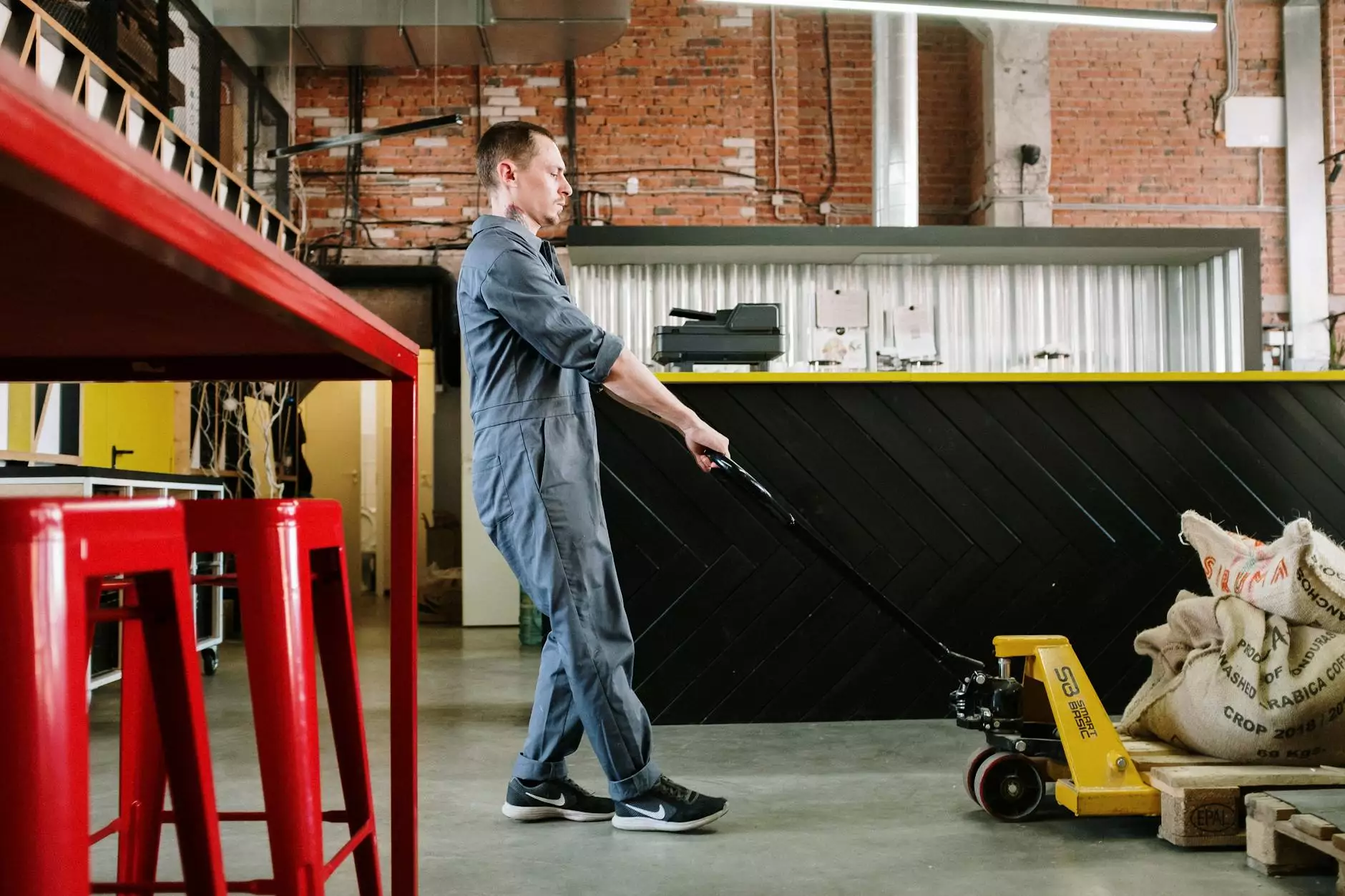
In today's competitive landscape, businesses are constantly searching for efficient methods to design, create, and deploy their products. The use of prototype molded parts is becoming increasingly pivotal in achieving this goal. This article delves into the intricacies of prototype molded parts, their significance in the metal fabrication industry, and how they can lead to enhanced efficiency and innovation.
The Concept of Prototype Molded Parts
At its core, prototype molded parts are preliminary versions of components produced to test a design's viability before mass production. These prototypes allow manufacturers to evaluate functionality, fit, and aesthetics. By utilizing advanced molding techniques, businesses can examine their product in a tangible form, making necessary modifications more straightforward and cost-effective.
Why Prototype Molded Parts Matter
Some of the key reasons why integrating prototype molded parts into the manufacturing process is crucial include:
- Risk Mitigation: Early testing reduces the chances of costly errors in mass production.
- Cost Efficiency: Identifying design flaws early leads to savings in resources and time.
- Improved Communication: Prototypes serve as effective tools for communicating ideas among team members and clients.
- Market Validation: Prototypes allow for consumer feedback before finalizing the product.
How Prototype Molded Parts Enhance Product Development
The integration of prototype molded parts in product development has transformed how businesses approach new designs. Here’s how:
1. Rapid Prototyping Techniques
The field of rapid prototyping has witnessed substantial growth with the advent of 3D printing technologies and CNC machining. Using these methods, manufacturers can create precise and accurate prototype molded parts quickly. This speed in the prototyping phase accelerates the overall product development timeline, allowing businesses to bring products to market faster.
2. Design Iteration
Prototyping enables designers to iterate on their ideas with immediate feedback. For instance, a team can quickly create multiple designs, evaluate them, and decide which direction to pursue based on practical insights gathered during testing. This iterative process ensures that the final product is not just theoretical but practically refined for the market.
3. Material Choices and Testing
Choosing the right materials is crucial for the performance of prototype molded parts. Manufacturers often employ various materials, such as thermoplastics and metals, to gauge their suitability for the intended application. Testing different materials helps in understanding their strength, durability, and potential application environments, thus refining the product further before mass production.
The Role of Metal Fabricators in Prototype Development
In the metal fabrication industry, the role of metal fabricators is essential in the creation of prototype molded parts. These specialists utilize various techniques to ensure that the prototypes meet the necessary specifications. Their capabilities include:
1. Precision Engineering
Effective engineering practices are crucial when creating high-quality prototype molded parts. Metal fabricators apply precision engineering to ensure that each prototype meets exact dimensional specifications, enabling reliable performance in the final product.
2. Custom Solutions
Many businesses require bespoke solutions tailored to their specific needs. Metal fabricators have the expertise to produce custom prototypes that align with unique project requirements, ensuring that the prototype accurately represents the intended product design.
3. Advanced Technology Implementation
The integration of advanced technologies such as laser cutting and robotic welding allows metal fabricators to produce high-quality prototypes efficiently. This technological edge gives businesses access to prototype molded parts that exhibit not just superior quality but also fast turnaround times.
Advantages of Using Prototype Molded Parts
Incorporating prototype molded parts into the design and manufacturing process provides numerous advantages:
1. Enhanced Product Quality
By identifying potential flaws in the design before mass production, businesses can ensure that their final products meet high standards of quality, which enhances customer satisfaction.
2. Cost-Effectiveness
Investing in prototyping can save significant amounts in production costs by minimizing the risk of producing defective products or components. Early identification of design flaws can prevent expensive recalls after launch.
3. Customer-Centric Development
With prototypes, businesses can engage potential customers earlier in the development process, gathering valuable feedback that leads to tailored final products which better meet their needs.
4. Competitive Advantage
Companies that utilize prototype molded parts effectively can differentiate themselves in the marketplace. Rapid development cycles allow these firms to innovate faster than competitors who rely solely on traditional design and testing methods.
Case Studies: Successful Implementation of Prototype Molded Parts
Examining real-world applications of prototype molded parts can provide valuable insights into their effectiveness:
Case Study 1: Automotive Industry
One automotive manufacturer leveraged prototype molded parts to develop a new vehicle model. The team created multiple iterations of key components, testing for safety, efficiency, and aesthetic appeal. This approach helped the company identify and resolve critical design issues well before production, resulting in a successful launch and positive feedback from consumers.
Case Study 2: Consumer Electronics
A consumer electronics company utilized rapid prototyping techniques to roll out its new gadget. By engaging with users through beta testing with prototype models, they received feedback that informed final design tweaks. This not only improved the product’s functionality but also ensured that it resonated with target consumers upon release.
The Future of Prototype Molded Parts
As technology advances, the future of prototype molded parts looks promising. Businesses can expect:
1. Advanced Materials
Ongoing research into new materials will allow for even greater customization and performance of prototypes. Innovations such as biodegradable plastics and high-strength alloys are shaping future possibilities in product design.
2. Integration with AI and Automation
Integrating artificial intelligence and automated systems into the prototyping process will streamline workflows, enhance precision, and reduce lead times. This fusion is set to revolutionize how prototypes are designed, tested, and refined.
3. Expanded Applications
The continual evolution of prototyping technologies will see prototype molded parts finding use in a broader array of industries, including healthcare, aerospace, and consumer goods. As industries recognize the benefits of prototyping, its adoption will only continue to grow.
Conclusion
To summarize, the significance of prototype molded parts in the manufacturing domain cannot be overstated. Their ability to facilitate design testing, improve product quality, and reduce costs makes them a vital component in modern manufacturing. As companies like Deep Mould continue to innovate in this space, the potential for growth and improvement in the industry is immense. By embracing the concept of prototyping, businesses not only enhance their workflows but also position themselves favorably in an increasingly competitive market.
For businesses aiming to stay ahead of the curve, investing in prototype molded parts is not just a choice; it’s an imperative.