Harnessing the Power of SLS Technology in Business
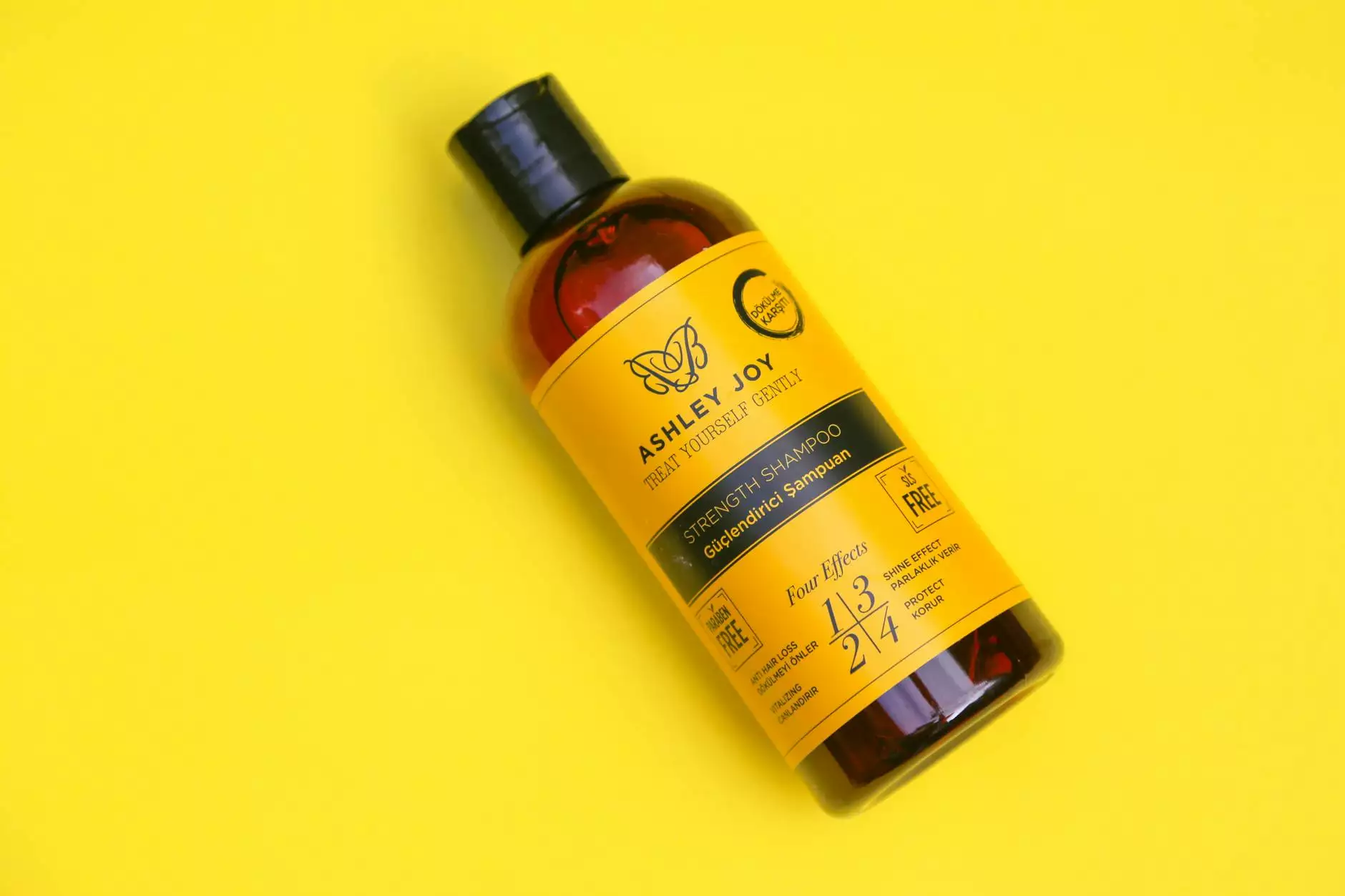
The world of business is in a constant state of evolution, driven by technological advancements that shape how products are designed, manufactured, and delivered. One such groundbreaking technology that is making waves across multiple industries is SLS technology, or Selective Laser Sintering. This innovative approach to 3D printing merges speed, precision, and versatility, positioning itself as a game-changer for businesses involved in art supplies, product design, and 3D printing. In this article, we will dive deep into what SLS technology is, its benefits, its applications, and how it can elevate your business strategy.
Understanding SLS Technology
At its core, SLS technology is a type of 3D printing that uses a laser to fuse small particles of plastic, metal, ceramic, or glass into solid parts. The process begins with a digital 3D model, which is sliced into layers by specialized software. The SLS machine then spreads a thin layer of powdered material across the build platform. A high-powered laser then scans the layer and selectively fuses the powder based on the layer's cross-section.
How SLS Works
- Layer Preparation: A layer of powdered material is spread across the build area.
- Selective Laser Sintering: The laser scans the powder, melting and fusing the particles together.
- Layer by Layer Construction: The process repeats, adding layer upon layer until the object is fully formed.
- Cooling and Removal: Once complete, the object is allowed to cool before being removed from the unused powder.
The Advantages of SLS Technology
If you're in the business of art supplies, product design, or 3D printing, the benefits of integrating SLS technology into your operations are manifold:
- Enhanced Precision and Detail: SLS technology produces highly detailed models, capturing intricate geometries and designs that are difficult to achieve with traditional manufacturing methods.
- Material Versatility: This technology supports a variety of materials, including durable plastics and metals, making it suitable for a wide range of applications.
- Complex Designs Made Easy: SLS allows for the creation of complex structures that are often impossible to manufacture using traditional methods, such as intricate lattices or internal channels.
- Reduced Waste: Unlike subtractive manufacturing that cuts away material, SLS uses only the required amount of powder and can reuse excess material, significantly reducing waste.
- Rapid Prototyping: Businesses can accelerate their product development cycles by quickly producing prototypes, facilitating faster feedback and iterations.
Applications of SLS Technology in Business
1. Art Supplies
Companies in the art supplies sector can leverage SLS technology to create bespoke tools and supplies tailored to artists' needs. For example, custom palettes, brushes, and sculpting tools can be designed with intricate detail, allowing for unique artistic expressions. Furthermore, SLS enables small batches of innovative art supplies to be produced without the need for large-scale manufacturing investments.
2. Product Design
In product design, SLS technology opens new avenues for innovation. Designers can create intricate prototypes that closely resemble final products, helping them to evaluate form, fit, and function before moving to mass production. This process not only saves time but also reduces costs associated with design errors. The ability to visualize products in 3D enhances collaboration among teams, ensuring everyone is aligned with the design vision.
3. 3D Printing
For businesses closely tied to 3D printing, integrating SLS technology elevates production capabilities. Companies can offer clients services such as on-demand manufacturing and mass customization. Whether producing unique consumer products or specialized components for industries such as aerospace or healthcare, SLS technology provides the flexibility and efficiency needed in the fast-paced world of 3D printing.
Case Studies: Successful Implementations of SLS Technology
Case Study 1: Custom Art Tools
An up-and-coming art supplies company adopted SLS technology to create a line of custom sculpting tools. By leveraging this technology, they were able to develop tools that conformed perfectly to the ergonomic needs of the artist. This led to a unique selling proposition that distinguished them in a crowded market, resulting in a 300% increase in sales within the first year.
Case Study 2: Rapid Prototyping for Product Development
A product design firm specializing in tech gadgets integrated SLS technology to streamline its prototyping process. This allowed them to reduce the time taken to go from concept to prototype from weeks to just a few days. The enhanced speed improved client satisfaction and facilitated quicker go-to-market strategies, ultimately leading to a significant increase in client retention rates.
Case Study 3: Customized 3D-Printed Parts
A 3D printing service provider that focused on low-volume, high-precision parts utilized SLS technology to cater to the aerospace sector. The ability to produce complex geometries made them the preferred choice for aerospace companies looking for lightweight, strong components. Their profits doubled as they captured a niche segment of the 3D printing market while maintaining a lean operation.
Challenges and Considerations for SLS Technology
1. Initial Investment Costs
While the benefits are substantial, it’s essential to consider the initial investment costs associated with acquiring SLS machinery and materials. Businesses need to conduct thorough financial analysis to ensure that the integration of SLS technology aligns with their long-term strategic goals.
2. Technical Expertise
Implementing SLS technology successfully requires a certain level of technical expertise. Businesses should invest in training their staff or hiring skilled professionals who can operate and maintain SLS printers. This expertise is crucial to maximizing the potential of the technology.
3. Material Limitations
Although SLS technology offers a wide range of material options, some materials may not be suitable for certain applications. Businesses need to conduct research and testing to ensure they select the right materials for their specific needs, taking into account factors such as strength, flexibility, and temperature resistance.
Future Trends in SLS Technology
The landscape of SLS technology is continually evolving, offering exciting prospects for businesses. Trends such as advancements in materials science, automation within the SLS process, and increased integration of artificial intelligence for optimized design and production are on the horizon. As these trends develop, businesses that stay ahead of the curve will have the opportunity to innovate boldly, ensuring they remain competitive in their respective markets.
Conclusion: The Path Forward for Businesses
In conclusion, SLS technology presents a vast array of opportunities for businesses across various industries, particularly in art supplies, product design, and 3D printing. By leveraging the advantages of this technology—enhanced precision, material versatility, and rapid prototyping—companies can not only improve their operational efficiencies but also unleash their creative potential. As you consider the future of your business, ask yourself: How can SLS technology transform the way you operate and innovate? With the right strategy and understanding, the possibilities are limitless.
For more insights into art supplies, product design, and 3D printing, explore our offerings at Arti90.